Industry News
First ZF wind turbine gearbox with connection to Schaeffler Cloud put into operation
10 Oct,2018 On the basis of the real loads from the operation of the wind power plant, Schaeffler and ZF use jointly developed expert models to produce analyzes and forecasts on the state of the transmission.
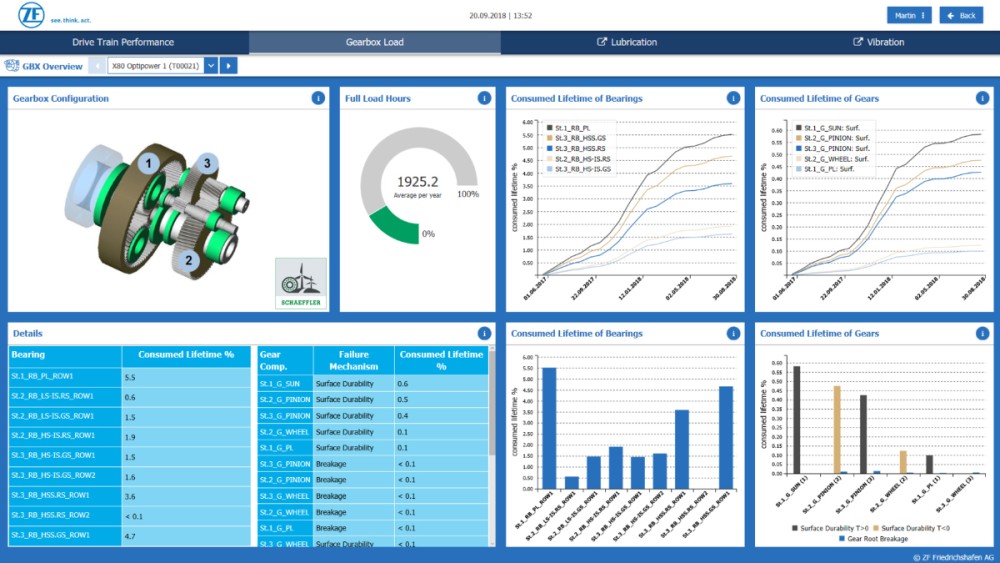
At the Hannover Messe Industrie 2018, Schaeffler presented a cooperation and development project with ZF Friedrichshafen for the wind energy industry. Sensor-equipped wind turbine transmits load data to a cloud-to-cloud solution from both companies during operation. The basic idea of the project is to make the ZF software solution for wind turbine transmissions available in an intelligent system together with the expertise of other specialists in a single platform. Wind farm operators thus receive an aggregated view of the transmission. Schaeffler is the preferred partner for rolling bearings and provides analyzes of rolling bearing loading. The assessment of the stress on transmission components is carried out by ZF. The project is openly designed so that other companies, such as B. a lubricant expert or a control provider can be integrated.
In the solution now installed, preprocessed data from the condition monitoring system and other sensors are transmitted to the ZF cloud, and torque and speed data are forwarded to the Schaeffler cloud. There, a detailed simulation model of the ZF transmission is implemented as Virtual Twin. The calculation results of the Virtual Twin are transmitted back to the ZF cloud and are available on the dashboard of the ZF software for monitoring the transmission status.
Extended planning horizon for wind farm operators
By monitoring the actual loads on wind power transmissions, ZF and Schaeffler are laying the foundation for developing new data-based models. Based on the available input variables, the lifetimes and the static load-bearing safety of the gearbox bearings are evaluated in a first step using the Virtual Twins - analogous to the procedure for the certified design of the bearings. In a next step, besides fatigue, further damage mechanisms can be considered in the future. This is necessary because the service life of rolling bearings in wind power applications is typically not limited by classic material fatigue, but by surface-induced damage (eg, excessive wear or contamination of the lubricant). Schaeffler has already developed an algorithm that can be used to calculate the risk of surface-induced damage. The transmission and testing of such new methods for the condition prediction of rolling bearings, especially in the field of wind energy, is part of the cooperation with ZF. By evaluating the calculation results of the Virtual Twin on the basis of load data, damaging operating conditions can be detected early on. Thus, it will be possible to clearly exceed the lead time for the initiation of maintenance measures compared to today's condition monitoring systems. In addition, appropriate countermeasures can be taken in good time to prevent critical operating conditions and thus extend the shelf life. Wind farm operators will thus have access to a tool that significantly expands their planning horizon.
Aligning the service life of bearings with product recommendations based on real data
Based on the actual cumulative load experienced by each bearing in the gearbox, Schaeffler will also be able to offer optimized product recommendations with a comparatively long lead time to the next maintenance interval. This can be a 1: 1 replacement of the respective bearing, an upgrade with a coating, a bearing with a high-performance material or a special heat treatment. Considered over the entire transmission, there is thus the possibility to better match the service life of all bearings in the transmission with each other.
The coming months will serve to test the installed IT infrastructure as well as the data transfer in practice. The collected experience with its technical, legal and economic challenges will be included in the later series production.